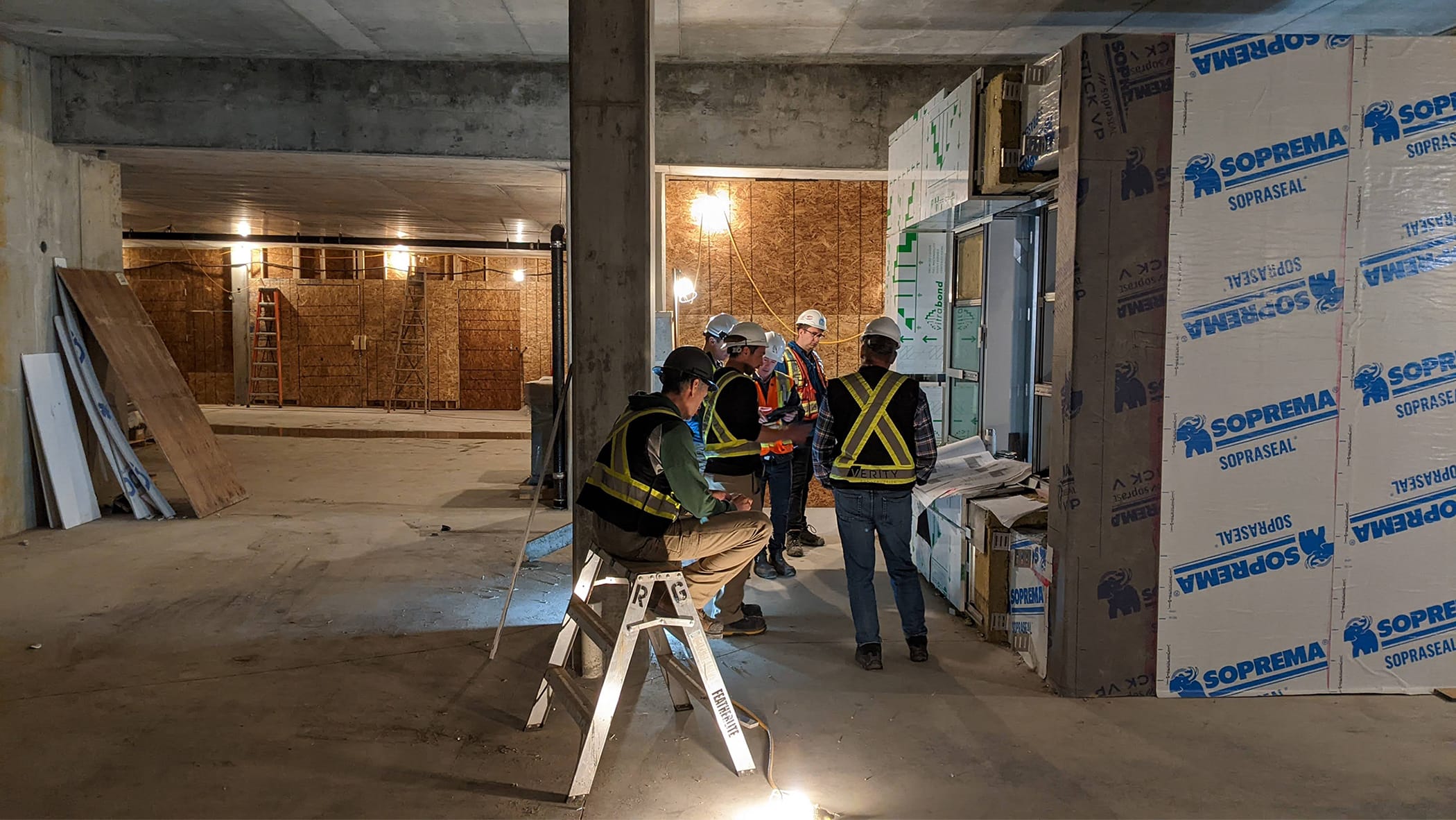
Constructed offsite, onsite, or in-situ, mock-ups make a difference...
This was a key takeaway the Cascadia Architects team had when on a discovery retreat to Seattle, WA. It was while visiting a peer-project site that we saw first-hand both the design and fiscal impact that adopting use of full-scale mock-ups could indeed have, (especially when reviewing envelope and cladding details for our projects).
Our own adoption of mock-ups has since become a relevant tool of our trade since then.
Why use full-scale mock-ups?
Depending on the scope, mock-ups are used in new designs when trying out new designs, or systems not previously tested or when combining multiple components together in order to ensure they work.
During the construction phase, it is typical to review envelope details after the first installation is underway and do a review on the building as a whole at that stage. The downside to this, is that if there are any sort of errors in materials or measurement—it can translate to additional (costly) changes needing to be made.
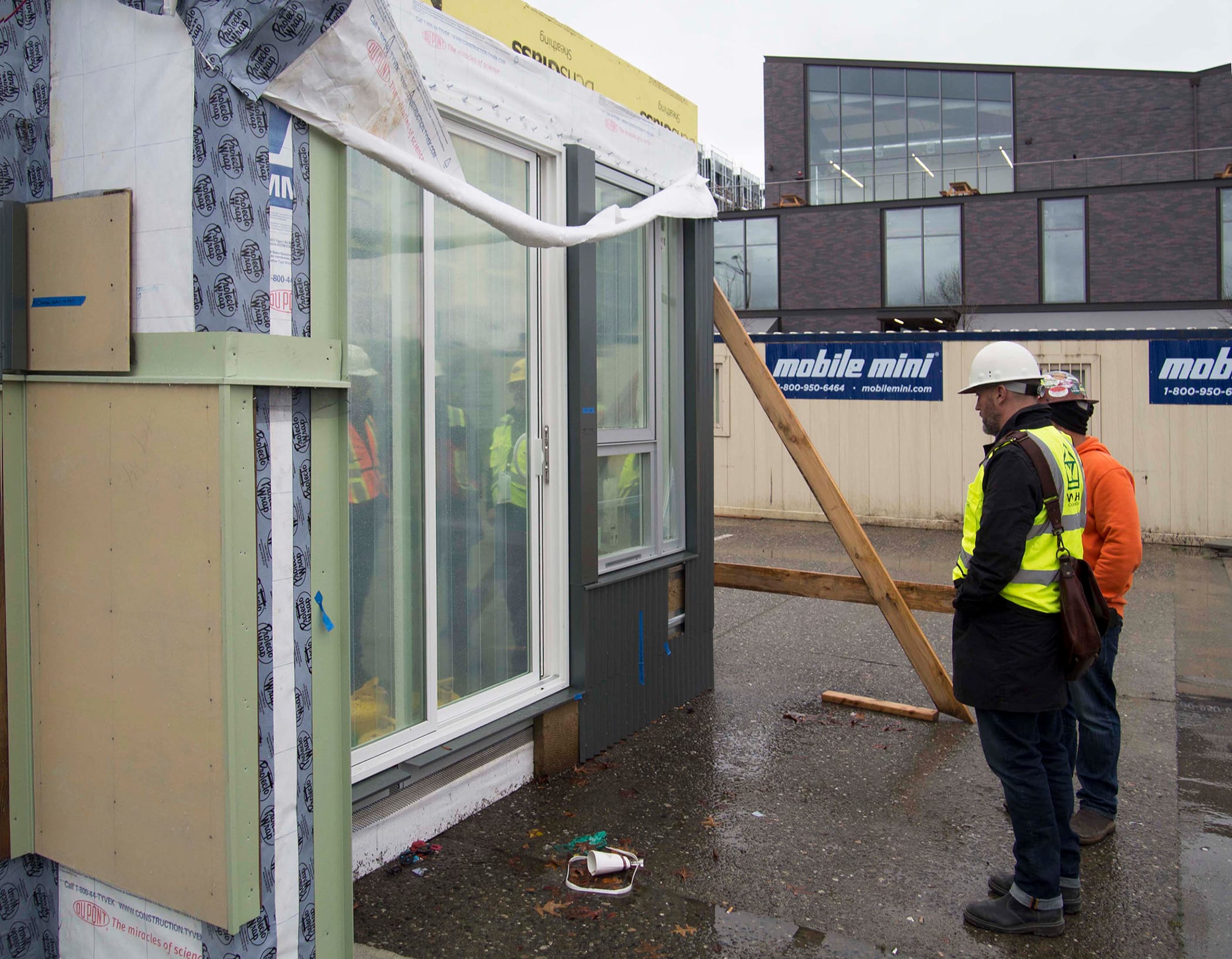
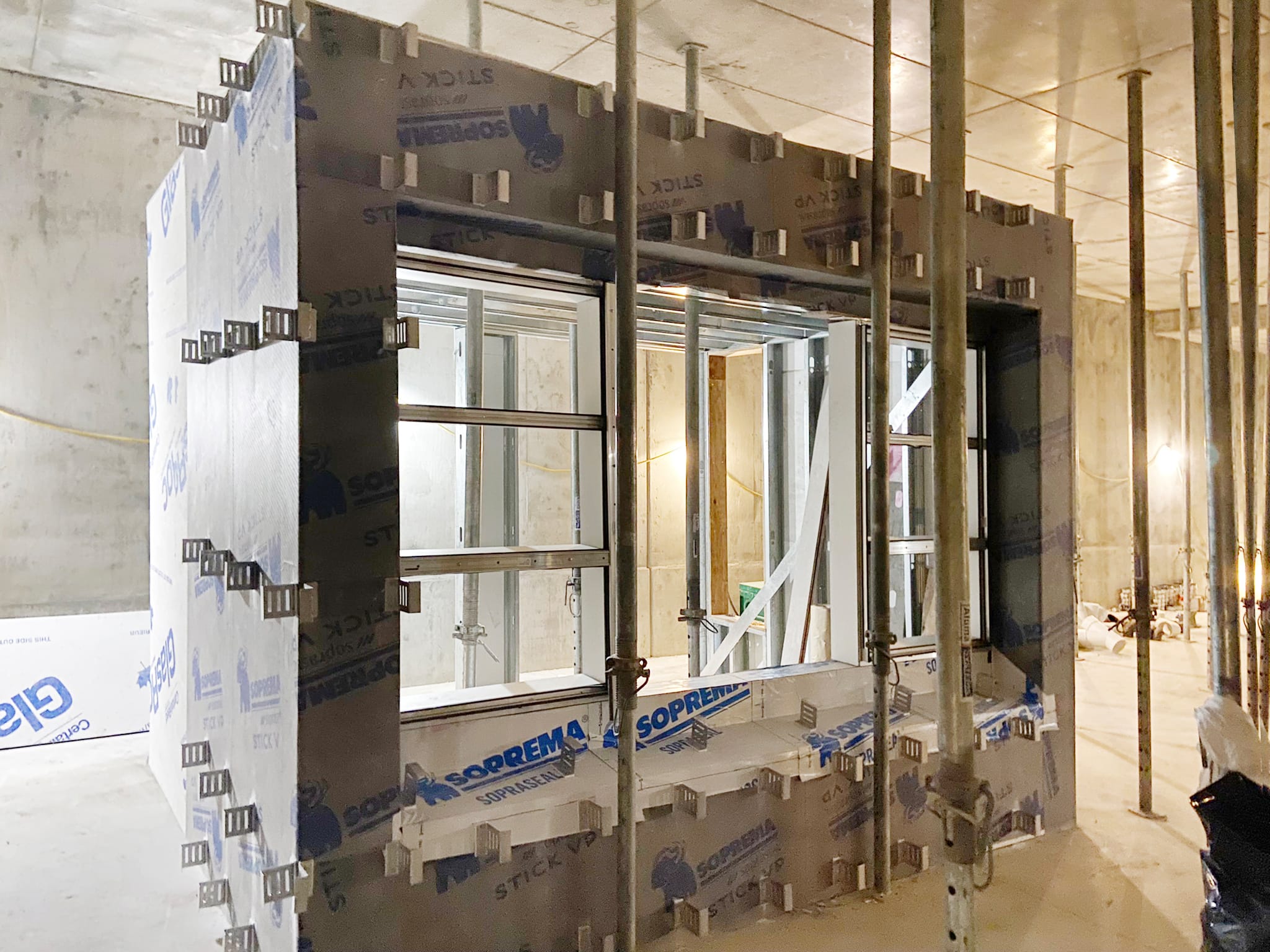
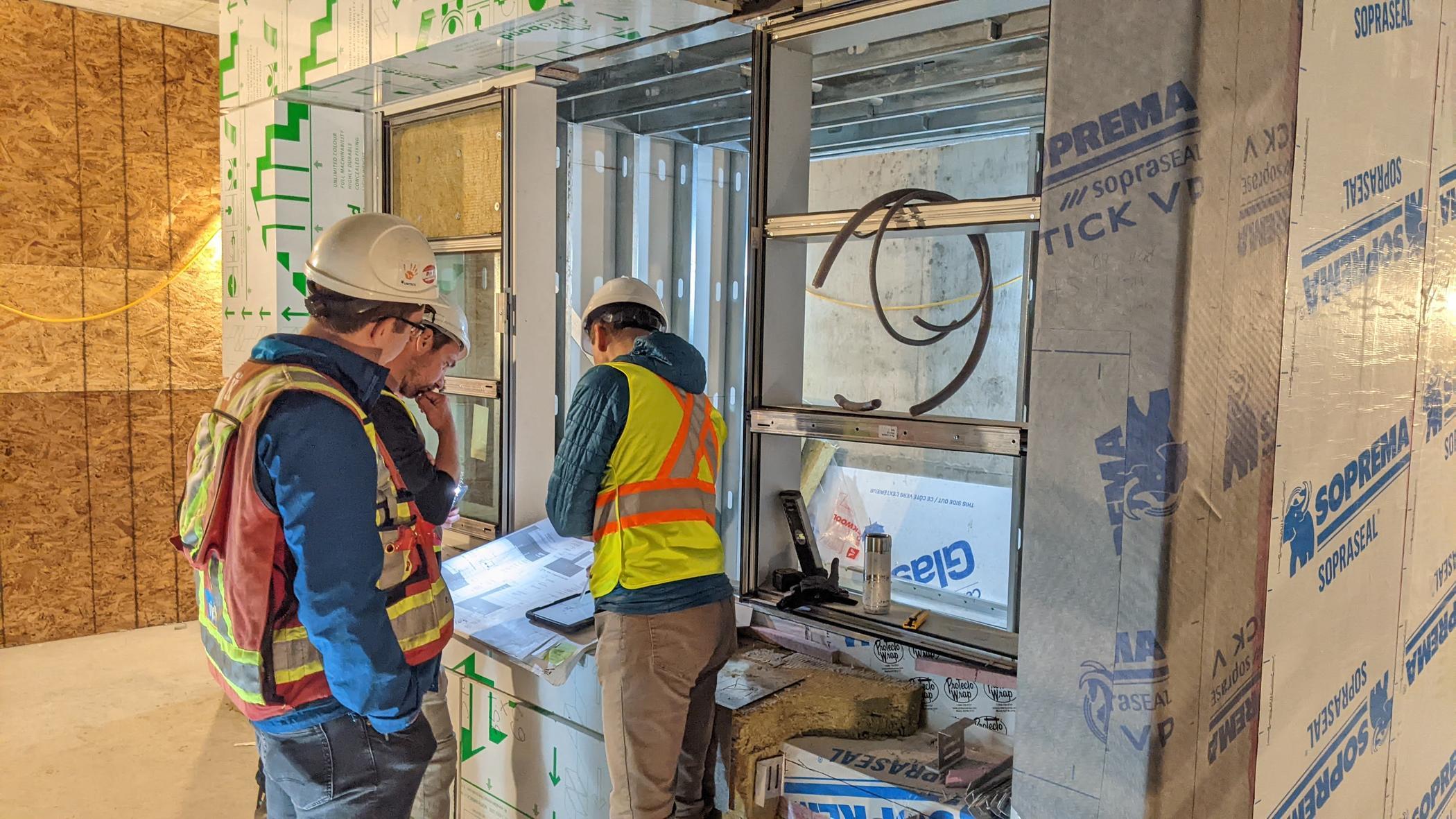
There are benefits in doing a full-scale mock-up to the in-situ reviews.
First attempts at a detail can require re-working, and if the architect is not on site after the first installation, it could mean the removal of installed material and pausing work for a fully mobilized crew.
A detail often requires close coordination of various trades to achieve specific performance and visual qualities. With a full-scale mock-up, this can be coordinated ahead of time.
Negative downstream impacts of early decisions are better resolved when mocking up all the layering of a detail before the first component is installed on the building (as shown in the close-up image shown below).
The full-scale mock-up acts as an orientation space for new trades arriving to the site, and can consequently assist with overall cost-effectiveness (labour).
Stand-alone mock-ups are constructed before work on the building envelope starts, so trades and consultants can work out details before teams are on-site....It is easier to make changes ahead of time—before issues arise 6 storeys in the air.
Onsite versus In-situ mock-ups.
Onsite mock-ups are usually smaller, helping to develop a benchmark through the construction phase by providing a strong visual example.
Performance testing can be incorporated into an onsite mock-up, though it's usually limited to compliance testing. In-situ mockups (often useful for trade coordination) are similar to onsite ones, with the benefit being that they can be incorporated within the construction.